FANI PLAST
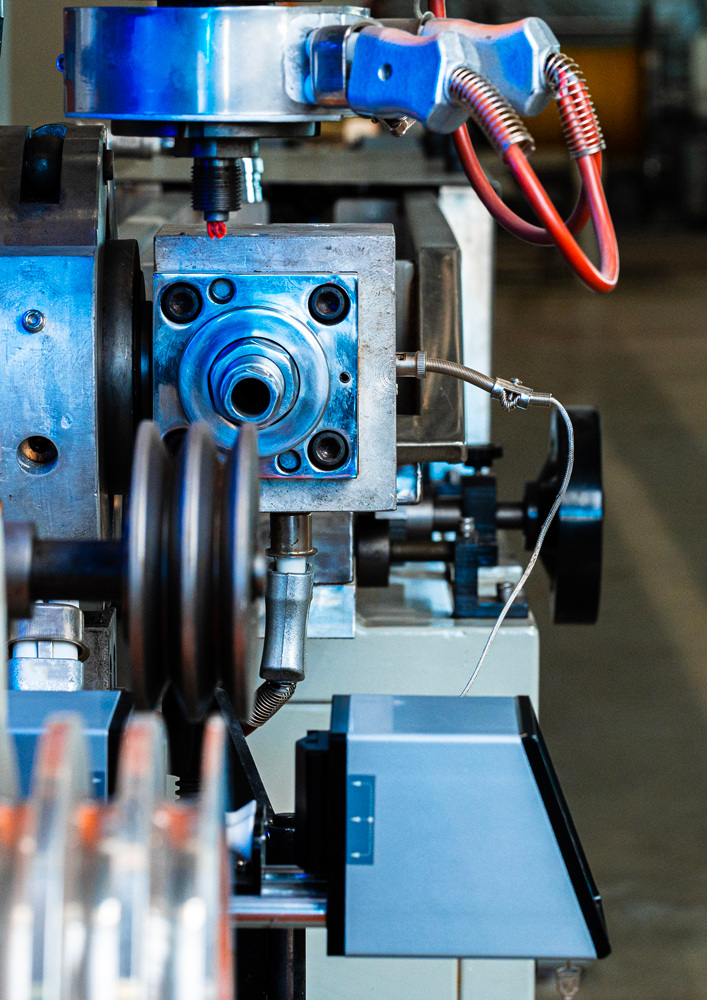
more than 60 years of experience
— FANI PLAST:
What we do
Our processing techniques generate quality products that meet the customer’s needs, starting from the recovery stage of plastic waste to its transformation into compounds suitable for molding or extrusion.
Recovery
We have the authorizations for the transportation, including by our own vehicles, and recovery of scrap and milled material derived mainly from industrial production waste, which is sorted, processed, and stockpiled in our warehouses.
We take your industrial waste, offering concrete solutions for its efficient reuse.
Mixing
The ground material is sent to the mixing department, where formulas are made according to the customer’s specific request. This critical step ensures that the material is perfectly suited to the needs of the items to be printed or extruded later.
Materials such as glass fiber, calcium carbonate, anti uv, antioxidants can be added to enhance the product. The material can also be colored using a masterbatch.
Drawing
During the drawing phase, the homogenized, additive-enhanced, and mastered material is transformed into high-quality regenerated granules through the following extrusion lines:
- one Tecnova single-screw die with overhead cutting and self-cleaning filter changer;
- two Icma San Giorgio twin-screw dies with plate filter changer and spaghetti cutter;
The added equipment of each machine, including filter changer and degassing pump, ensures a tailor-made product suitable for a wide variety of industrial applications.
Material analysis
In order to ensure that the quality requirements expressed by customers are fully met, Fani Plast uses an in-house laboratory, equipped with specific instrumentation:
- Melt Flow Index measurement;
- Press for molding specimens
- IZOD Universal Pendulum (impact strength analysis);
- X-Rite spectrophotometer (color control).
- Muffle (ash percentage determination).
The analyses are accompanied by a detailed data sheet, ensuring transparency and reliability.
Bagging
After the drawing process, the granules are screened through a vibrating sieve and then conveyed to a final storage silo. Finally, the material is packaged and can be supplied in 25 kg bags (made of paper, polyethylene, or aluminum) or in big bags, according to the specific requirements of the customer.